Dr. Elena Vagnoni, scientist and lecturer at EPFL and XFLEX HYDRO Scientific Coordinator, is overseeing the coordination and monitoring of XFLEX HYDRO’S demonstrations. Read her progress update below.
To date, all demonstrations in XFLEX HYDRO have been focused on performing initial studies. These are essential to ensure robust implementation of the innovative technological solutions at the hydropower sites.
The main results of the studies completed so far are summarised below.
- Z’Mutt: a pumped storage hydropower plant equipped with a 5 MW reversible pump-turbine. This demonstration’s objective is to show an increase in flexibility by implementing variable speed technology using a Full-Size Frequency Converter (FSFC). Numerical simulations have been performed to select the best operating sequences to improve the response time of the machine during transient operations, as illustrated in Figure 1. Next steps are further numerical simulations and reduced-scale modelling to test and consolidate the operating sequences.
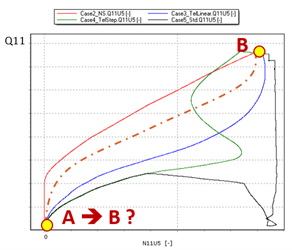
- Frades 2: a pumped storage hydropower plant with two 390 MW reversible pump-turbines. This demonstration’s purpose is to show the improved flexibility of variable speed units equipped with Doubly-Fed Induction Machines (DFIMs) and hydraulic short circuit technology. The initial study has highlighted the benefit of this technological solution in noticeably extending the operating range of the two hydroelectric units, as presented in Figure 2. This has been achieved by performing extensive computational fluid dynamics (CFD) numerical simulation of the simultaneous operation of the two units. Next steps are to implement the control of this technology and define the optimal operating sequences to increase the provision of ancillary services to the power system.
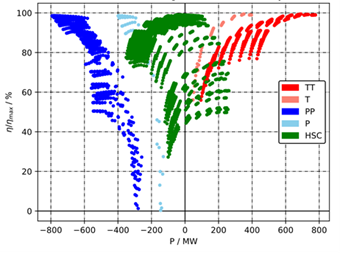
- Grand'Maison: a pumped storage hydropower plant featuring twelve 150 MW units, consisting of four Pelton turbines and eight reversible pump-turbines. This demonstration’s goal is to implement hydraulic short circuit, using new turbine runners and advanced control techniques for efficiency and flexibility improvements. Numerical simulations have been performed to validate feasibility and identify the hydraulic and structural constraints of this technology’s implementation. Next steps are preliminary on-site tests and the smart control of the unit operating in hydraulic short circuit.
- Alqueva: a pumped storage hydropower plant with four 130 MW reversible pump-turbines. This demonstration’s objective is to demonstrate low-CAPEX opportunities to improve flexibility by implementing hydraulic short circuit and advanced control strategies. Initial studies investigated the technical capability of the units to implement hydraulic short circuit. Specifically, the critical operations and flow conditions have been assessed through numerical simulations. This is informing definition of the procedure and the necessary validations for on-site testing, to fully assess the benefits and risks of this technology. This activity, together with the control system implementation, is being performed as a next step.
- Alto Lindoso: a reservoir storage hydropower plant equipped with two 317 MW Francis turbines. This demonstration’s goal is to implement low-cost opportunities for a high head plant to extend its operating range and optimise power flexibility using advanced joint control. Numerical simulations highlighted the possibility of extending the operating range, with improved knowledge of the load cycles based on flow conditions and fluid-structure interactions at part load operation. This will help define the operating condition to be tested and development of a robust control system.
- Caniçada: a reservoir storage hydropower plant featuring two 35 MW Francis turbines. This demonstration’s aim is to evaluate and compare flexibility options for a medium scale plant, including a potential conversion to variable speed. To date, numerical simulations of the flow and the structural load of the machine have been performed, characterising the dynamic behaviour of the flow and the machine components. These initial results are being consolidated and validated with experimental on-site tests.
- Vogelgrun: a run of river hydropower plant equipped with four 39 MW Kaplan units. This demonstration tackles the hybridisation of one of the units with a Battery Energy Storage System (BESS). This adds energy storage to share response capability with the hydraulic unit and uses a master control to optimise flexibility services and maintenance. The initial studies focus on defining the ideal battery size (about 2 per cent of the nominal power of the hydroelectric unit) and its control, as well as estimating the benefits in terms of wear reductions on the turbine. One of the first results includes outputs from the numerical simulations, which identified stresses on the runner components more prone to fatigue damage, shown in Figure 3. The next step is validation of these results by performing on-site measurements, currently underway, to inform implementation of the optimal control and monitoring of the hybrid unit.
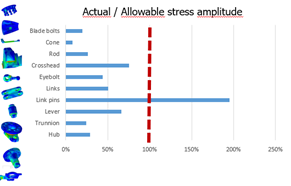